Exploring the Range of Our Business Capabilities
- Achieved a milestone in 2019 by processing over 38 million FBM, demonstrating our operational efficiency.
- Equipped with the capacity to kiln dry over 1.0 million FBM at once, ensuring timely delivery of large orders.
- Poised for growth with the potential to expand our kiln drying and lumber remanufacturing capabilities.
- Serving a diverse customer base, reflecting our adaptability to various industry needs.
- Specializing in a variety of woods including Douglas Fir, Western Hemlock, Western Red Cedar, Yellow Cedar, and SITKA Spruce, offering a wide selection of quality wood products.
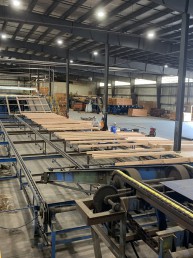
TWIN BAND RESAW
This is a dual-band Kockums-Cancar computer-adjusted resaw system, capable of processing materials up to 14" x 36" in size and 24' in length using band saws. The resaw line features a tilt hoist that supplies a front-end trimming/grading station and delivers final trimming and grading after the resaw process. The system includes a manually operated pull transfer chain and an end stacker, which efficiently directs the maximum quantity of same-grade and same-length products from a specific work order.
McDONAGH RESAW/LEADERMAC MOULDER
Our newest production line features a 48" single band, fixed McDonough Resaw that feeds directly into a 6 head Leadermac moulder. The single band resaw is strategically aligned to allow product to seamlessly feed into the moulder, surface the result on any or all sides, product fascia or pattern stock, optimizing the workflow. We also have the ability to bypass the resaw and feed the moulder directly.
The line is equipped with a covered tilt hoist that feeds the resaw/moulder and a second covered tilt hoist that feed the moulder directly. There is also a 3 saw trim station that allows DET, cut to custom length or cut in two. The inline packaging station is set up to facilitate end-capping and mini-bundling (if required) as well as paperwrapping with attached dunnage.
KILN DRYING / HEAT TREATING
The kiln facility is housed in a tilt up concrete building with concrete flat roof. The kiln consists of seven (7) independent side loading chambers which can accommodate 5 rows of stacked lumber for drying. Of the 7 kilns, three (3) are rated for 175,000 board feet and four (4) are rated for 100,000 board feet. Each kiln has its own manual controller which directs the requirements for direct gas fired heat based on wet and dry bulb temperature settings. The kiln drying process benefits from two (2) boilers that produce steam for lumber conditioning. Significant experience in the management group provides comprehensive drying schedules to ensure customers continue to be highly satisfied with drying results.
Southcoast has relatively new kiln PLC controllers designed, built, and installed that utilize new VFDs to control fan speed during drying schedules in conjunction with a leading edge energy management system. This new technology enhances our kiln drying performance.
PLANING - GRADING & TRIMMING WITH END STACKING SYSTEM
Our 610 Stetson Ross planer is equipped with a tilt hoist that includes de-sticking capabilities, ensuring optimal preparation of kiln-dried lumber before it enters the planing process.
The planer's outfeed leads to a value-adding trimming system, manned by two certified lumber graders. Their expertise allows us to upgrade the lumber, maximizing both its value and fibre recovery.
To streamline the sorting process, we have a pull transfer chain and an end stacker in place. This system efficiently directs high volumes of lumber of the same grade and length, as per specific work orders, ensuring a smooth and efficient workflow.
WEINIG MOULDER
Our Weinig H23 line features a 7 head moulder feeding a grading table manned by a certified lumber grader allowing to accurately grade and package to customer specifications.
LUMBER WRAPPING, LABELING, PACKAGING
At Southcoast Reman, we prioritize quality in every aspect of our operations. We use top-tier lumber wrap for our products, or, if preferred, we can apply a customer's own lumber wrap featuring their company logo. Our commitment to precision and organization extends to our labeling process. We generate labels through the LISA inventory management system, ensuring each load is accurately labeled either as it passes through our packaging system or upon completion of kiln drying.
CAPACITY TO PROVIDE PEFC AND FSC CHAIN OF CUSTODY AGREEMENTS
In the past, Southcoast Reman held its own PEFC certification. However, the current standards no longer necessitate a custom lumber remanufacturer to possess an individual certificate. Despite this, our customers require us to uphold both PEFC and FSC chain of custody agreements through our process control and inventory management system. We are also subject to their audit requirements. Our business model is built on the principle of maintaining and verifying the integrity of our customer's wood, ensuring we meet and exceed industry standards and customer expectations.
CONTAINER LOADING FOR PROCESSING CUSTOMERS
Southcoast Reman weighs all loads in advance of both dock container loading or regular container loading and is highly efficient at turning trucked containers around with minimal delay. Our weigh scale is certified, and we provide a weight ticket per SOLAS regulations.
The operation does not run an off load, storage, reload business, but is focused solely on servicing shipping requirements for our customers that process (remanufacture or kiln dry) at our site.
LISA LUMBER INVENTORY MANAGEMENT SYSTEM
Southcoast Reman uses LISA, a tried and proven lumber inventory management system. We have established a mechanism to have our customers, through their operation or their custom cut sawmill, initiate a dynamic tag transfer for all in bound lumber products thereby ensuring the accuracy of transferred volumes and avoiding any unnecessary errors in re-entering data to Southcoast’s inventory system.
LUMBER STORAGE CAPACITY BASED ON EFFICIENT CUSTOMER INVENTORY TURNS
Southcoast Reman usually operates with an inventory of customer lumber between 4.5 and 6.0 million board feet. A portion of that volume can be stored under cover for short periods prior to remanufacturing . It is important that customers continue to move their lumber inventory to minimize exposure to the weather and subsequent loss of value, even if it is paper wrapped.
CUSTOMER PRODUCT SECURITY
Southcoast Reman’s property is completely fenced and has sixteen (16) video surveillance cameras and interfaced motion detection systems that are monitored continuously when the operation is not staffed.